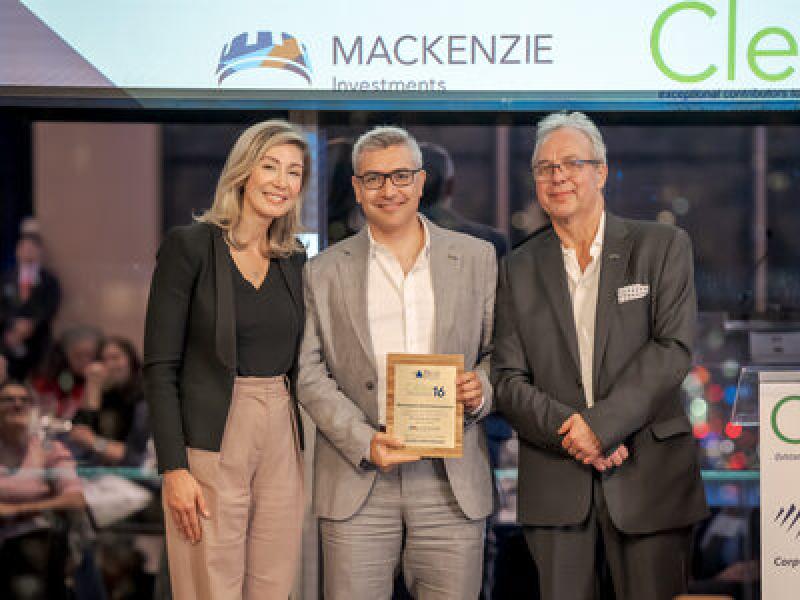
Vancouver-based pH7 Technologies Inc. has been recognized as a 2024 Clean50 honouree and as a Clean16 award winner in the research and development category, thanks to its closed-loop process for extraction of critical metals and minerals.
The company states its solvometallurgy process (using non-aqueous solutions to extract metals) results in a net 99 per cent reduction in carbon dioxide emissions, a 95 per cent increase in energy efficiency, zero toxic releases, no wastewater and near-zero water consumption relative to industry norms.
This results in metals like platinum, palladium, iridium, copper, nickel and more.
Founder and CEO Mohammad Doostmohammadi was inspired to create the company from his experiences being born and raised in Iran.
“I saw how people are struggling with the water over there, having been involved as a mining engineer (and) chemical engineer. Having garbage, lots of wastewater treatment plants, lots of mineral processing, mining processing that generates lots of wastewater, and that wastewater is not easy to treat,” Doostmohammadi told Sustainable Biz Canada in an interview.
“All of these experiences led me to found pH7, with one mindset: designing extraction processes without generating any wastewater.”
pH7 and Clean50
Canada’s Clean50 Awards, founded in 2011, are announced annually by Delta Management Group and the Clean50 organization to award 50 individuals or small teams across 16 different categories who have done the most to advance the cause of sustainability. This year’s honourees were chosen from a pool of over 1,000 – with advice from internal researchers and external advisors.
The leader in each of the 16 categories — in this case, Doostmohammadi — is also declared part of the Clean16 list, recognizing them as the top contributors in their respective categories. Other members of the Clean16 include employees from Nexii Building Solutions Inc., Toronto Hydro, Purolator Inc., BDC Capital, Capstone Infrastructure Corporation and more.
“Our current process is focusing on end-of-life materials. So spent catalysts from various industries that they have loaded with critical metals, vital for especially hydrogen energy and hydrogen technologies,” Doostmohammadi said.
“We extract these metals from different spent catalysts. (We) reuse these metals into hydrogen membranes, membranes for electrolyzers, for electrodes and different parts and components of hydrogen technology.”
The company currently receives approximately 500 kilograms of spent catalysts per day at its Metro Vancouver facility. Doostmohammadi explained pH7 largely gets its feedstock for its modular process from original equipment manufacturers (OEMs) in the U.S.
“The catalyst has about three to five years of life. OEMs send it back to us, we reprocess it, extract valuable metals and critical metals out of them,” he said. “We give the metals to OEMs and they reuse it to produce new catalysts (for) new membranes and different applications.”
pH7’s future
Earlier in March, pH7 closed a US$16 million Series A funding round featuring investors TDK Ventures, Pangea Ventures, BASF Venture Capital, FM Capital, Collaborative Fund and Rhapsody Ventures Partners.
From the funding, the company is building a demonstration plant ten times larger than its current one, also located in Metro Vancouver, capable of processing five tonnes of spent catalysts per day. It is scheduled for completion in 2024. The company's current demonstration plant can process up to 500 kilograms per day.
Doostmohammadi also mentioned plans to add demonstration plants in the U.S. and Europe. Naturally, that also involves plans to grow the company’s roster.
“Right now, we have 30 people. And I believe by next year, we're going to be minimum 50 to 60 people,” Doostmohammadi said. “We need to hire in all aspects of the business from operation (to the) finance team, so all of our teams are actually growing right now.”
He explained that by 2035, global demands for critical minerals and metals will multiply. Cobalt demand will double, nickel demand is set to triple, while demand for lithium, platinum and iridium will be ten times higher.
pH7 is working on making its modules more efficient, more environmentally friendly and more economical. Another part of its research and development includes expanding the closed-loop process to incorporate other raw materials.
“We are developing different platforms for copper, in both recycling and mining. We are developing platforms for end-of-life electronic waste and printed circuit boards recycling, (to extract) copper, gold, silver and other precious and critical metals from those materials as well,” Doostmohammadi said.
“We’re developing a process for black mass lithium-ion batteries. So we want to establish these closed-loop processes for all of our industries, all of our critical metals.”