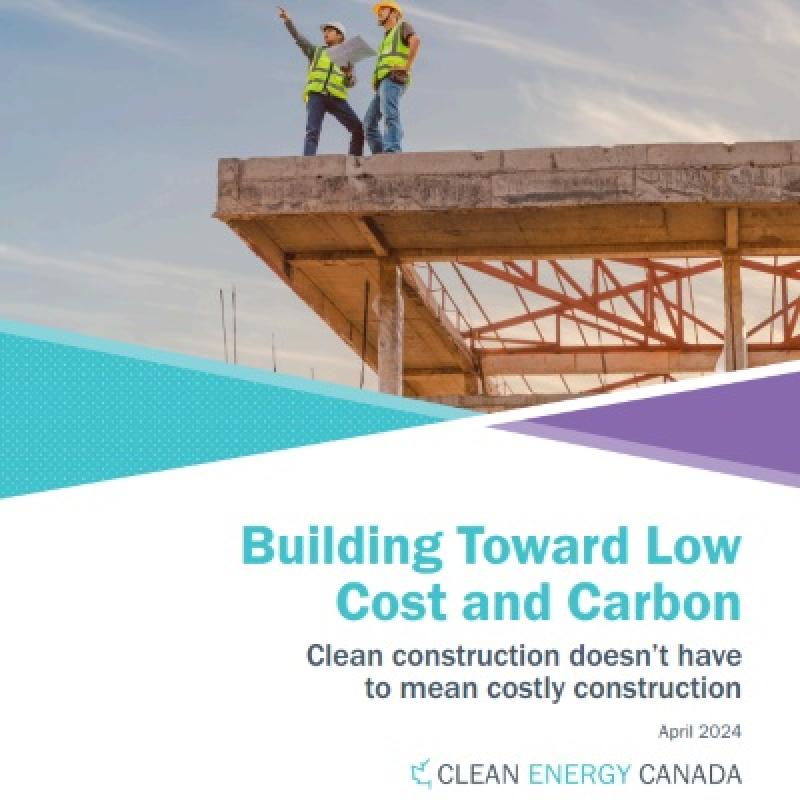
A home-building boom can be achieved with made-in-Canada, low-carbon materials that do not significantly raise construction costs, a report by Clean Energy Canada suggests.
With millions of new homes needed to address the country’s housing shortage, the Vancouver-based think tank says the enormous amount of concrete, steel and drywall to supply the construction will come at a significant climate cost.
But that can be offset with sustainably made materials for virtually the same cost. The design stage is where carbon and costs can be further pared down with no sacrifices to safety.
“We were honestly surprised how many options were available at market rates,” Jana Elbrecht, the author of Building Toward Low Cost and Carbon and a policy advisor for Clean Energy Canada, told Sustainable Biz Canada.
The materials can be made in Canada with low-carbon technologies, building up a domestic industry and serving as an export advantage amid increasingly volatile U.S. trade policy.
Reducing carbon with little or no cost increase
Clean Energy Canada looked at five commonly used construction materials — concrete, structural steel, rebar, drywall and insulation. Due to their production, transportation, use in construction and disposal, the materials carry varying degrees of embodied carbon, which makes up a significant portion of a building’s greenhouse gas emissions.
With the help of Canadian firm Chandos Construction, Clean Energy Canada compared the traditional and low-carbon building materials on price and pollution from recently constructed projects in Ontario, British Columbia and Alberta.
Most materials can be replaced with lower-carbon alternatives that have little to no increase in price, the two organizations discovered.
For example, concrete that embodies up to 32 per cent less carbon can be purchased — depending on the product — for either the same price or a premium of up to 16 per cent. The carbon reductions for drywall products range up to 55 per cent, with pricing virtually identical to conventional products.
The cost premiums overall were negligible, the report states. For the budget of one multimillion-dollar project, it added up to less than $2,000 in extra costs.
“What we’re trying to show here is we can already get lower-carbon materials at no additional price,” Elbrecht said, without needing to wait for innovations such as carbon-negative cement. Cement made with a waste material like fly ash, which reduces carbon emissions in concrete production compared to Portland cement, is already available.
Access to lower-carbon materials was generally not a problem in the case studies Chandos and Clean Energy Canada examined.
How design can further pare down carbon and costs
Further efficiencies can be realized before construction starts. Clean Energy Canada collaborated with Toronto-based architecture firm Ha/f Climate Design on ways buildings can be designed to use less materials. It means paying less, producing less carbon and shortening construction schedules.
Ideas such as a pitched roof made of low-carbon materials instead of a flat roof for a townhome can add up to removing over a quarter of the embodied carbon compared to typical architecture.
Above-ground parking is a more sustainable alternative to underground parking, Elbrecht said. This alone would cut the embodied carbon of a midrise housing complex by 16 per cent.
Clean Energy Canada is not advocating for lax safety standards, she said, but recognizing structures can overuse materials. Thinner concrete slabs will still meet safety requirements while reducing carbon, the report states.
Elevating domestic manufacturing
Though cost is argued to be a minor issue when adopting sustainable materials, Clean Energy Canada acknowledges there will likely be some hurdles.
Project planners may need more training. Low-carbon concrete could come with changes such as having a longer curing time than the conventional counterpart. City building codes can prevent use of the efficient designs.
But there are solutions: the design choices in the report can shorten timelines; early coordination with all parties helps with timely delivery; building codes can be reformed to be performance-based rather than prescriptive.
Despite the apparent advantages, the sustainable choices remain a small part of the market. The Cleantech Group found only three per cent of global cement production in 2023 was low-carbon cement.
“I think we should not undercount the effect of, ‘This is the way we’ve always done things.’ Change takes time,” Elbrecht said.
Buy Clean procurement policies that demand reductions in the embodied carbon of public projects can upend this dynamic, she said. This will boost the use of low-carbon materials and extend a helping hand to startups which are developing these sustainable materials, Elbrecht said.
A Buy Clean strategy for public construction projects could result in up to four million tonnes of carbon emissions being avoided by 2030, the report states.
Elbrecht hopes more governments, particularly at the provincial level, will adopt such policies.