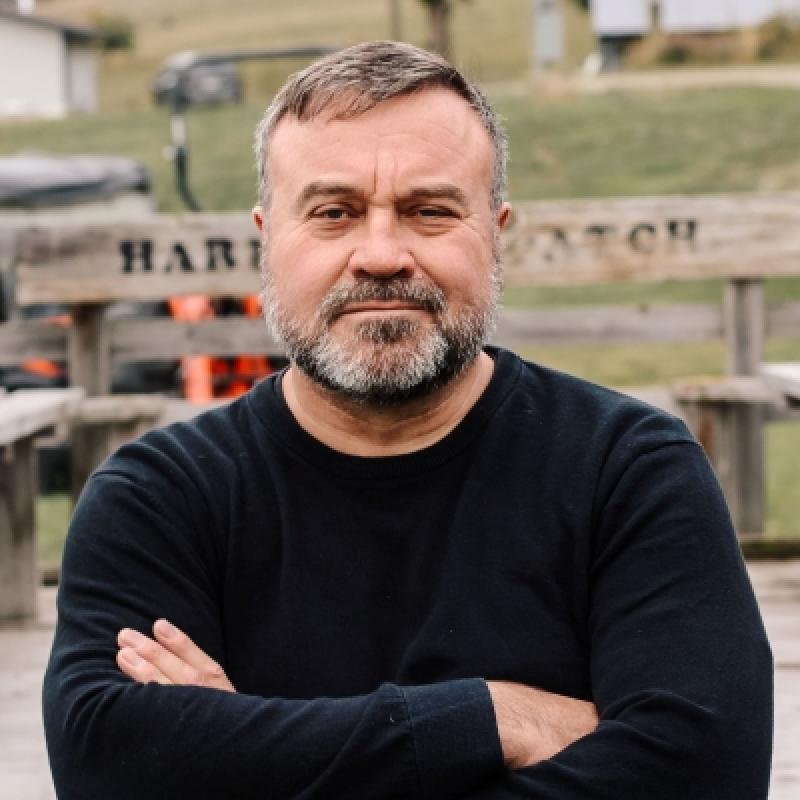
GUEST SUBMISSION: Unless you’re intimately familiar with cement production, odds are the cement industry’s nowhere near your carbon footprint radar, but it’s a top contributor.
The production of Portland cement (the concrete industry standard) creates roughly seven per cent of global carbon dioxide (CO2) emissions, which is unsurprising when you realize for each pound of cement produced, nearly a pound of CO2 is emitted.
More than four million metric tons of cement have been produced globally each year for the last decade. Cement serves as a binder in concrete, the most widely used building material in the world.
Replacing current cement practices isn’t easy – but it’s also not impossible. Low carbon cement companies have raised hundreds of millions in funding over the last few years as they clamour to be the first to market with a product that checks all the boxes. Some are replacing ingredients; some are introducing carbon capture or “sequestering” technology. When you understand the problem, it’s easier to navigate the potential solutions.
Demand for cement is only growing – and a 1:1 CO2 production practice is unsustainable
Global CO2 levels have grown significantly over the last 125 years – from 300 ppm (parts per million) to 420 ppm since 1900. That’s 40 per cent more CO2 in the air today, largely due to the use of fossil fuels for industrial efforts, energy, transportation and yes, cement production.
Breakdown of cement's CO2 footprint
Portland cement represents roughly 95 per cent of the cement produced in the United States, and production practices create a nearly 1:1 ratio of cement to CO2. If that’s not enough reason to make a change, some key ingredients are getting harder to source.
Shifting from our current production practices isn’t going to be simple or easy. When you change the ingredients, you change the recipe…and you change the flavour. And yet, that’s essentially what we’re talking about: changing the cement recipe without reducing the strength or performance of concrete.
Why does Portland cement generate so much CO2? Production starts with a “raw mix”, with limestone (calcium carbonate, or CaCO3) as the key ingredient. When the raw mix is heated to 900 C, the limestone transforms into calcium oxide (CaO) and CO2, and 44 per cent of the limestone’s weight is converted to CO2, released out of the kiln stack. That’s part one of cement’s CO2 footprint.
Next, the raw mix is heated to 1,500 C, producing a clinker. The heating process requires a massive amount of energy, which often comes from the burning of fossil fuels – part two of cement’s CO2 footprint. Finally, the cooled clinker is combined with a small percentage of gypsum and ground up into a fine powder, resulting in cement, which is then mixed with sand, rocks and water to create concrete.
The climate’s changing, and with it the availability of certain materials.
Some materials can be used to partially replace cement. They’re often referred to as “supplementary cementing materials” or “SCM”. Fly ash, a byproduct of burning coal, is the most commonly used SCM in cement production. It’s not particularly environmentally friendly. Steel slag is another commonly used SCM. More on both below.
Fly ash as an SCM
Coal is primarily composed of carbon. When coal burns, the carbon (C) reacts with oxygen (O) in the air, resulting in energy, in the form of heat and light – and CO2 in the atmosphere.
It’s why the federal government signed agreements in 2016 with the provinces who still have coal burning plants. Alberta and Saskatchewan committed to phase out coal-fired power by 2030, and Nova Scotia has committed to 2040 but has set a goal of achieving 80 per cent renewable energy by 2030.
Good news for the environment, bad news for cement. In the early 2000s, Alberta generated an estimated one to 1.5 million tons of fly ash; as of 2024, Alberta has stopped burning coal to produce electricity. Cement companies who previously sourced their fly ash from Alberta are now drawing from multiple sources around the world – or digging up old piles of buried fly ash which comes with its own related issues. In short, this SCM source is drying up.
Steel slag as an SCM
The other go-to SCM, steel slag, is also in short supply as steel production practices change. Standard steelmaking produces an abundance of CO2 emissions; producing one ton of steel releases about 1.85 tons of CO2.
New processes include using electric arc furnaces and hydrogen burning, which have smaller carbon footprints and produce significantly less (or no) steel slag. Algoma Steel, in Sault Ste. Marie, Ont., is replacing their legacy coking coal and blast furnaces with electric arc furnaces. This change will reduce the plant’s carbon footprint by 70 per cent.
Low carbon cement options: New ingredients, supplementary material, and sequestration
Something has to change. Cement production is generating an unsustainable amount of CO2, and key SCMs are much harder to access.
Low carbon cement solutions could replace fly ash or steel slag with a sustainable SCM alternative with a smaller carbon footprint. It might also introduce a new production process, emitting less CO2 – or even adding it back into the cement, sequestering it. There are solutions which inject CO2 into fresh concrete, underground or even in plants, soil or aquatic environments.
Still other solutions seek to reduce or replace limestone in cement, which works as long as you don’t alter the recipe too much – engineers aren’t going to accept an inferior product when it comes to keeping people safe on bridges and in buildings.
Regardless of what the solution claims, look at their whole process. If an organization claims to sequester CO2, where is the CO2 coming from? Are they sequestering CO2 at source, or purchasing compressed CO2 and transporting it? How much do they sequester? How much are they releasing into the atmosphere?
At the end of the day, cement practices need to change – because demand won’t.
Cement demand isn’t going anywhere. Engineering standards will not be compromised. And the cement industry cannot maintain its current footprint. We’re going to need multiple solutions to make a sustainable change. Just be sure to look critically at the information prospective solutions are sharing – and what they aren’t – before you invest.