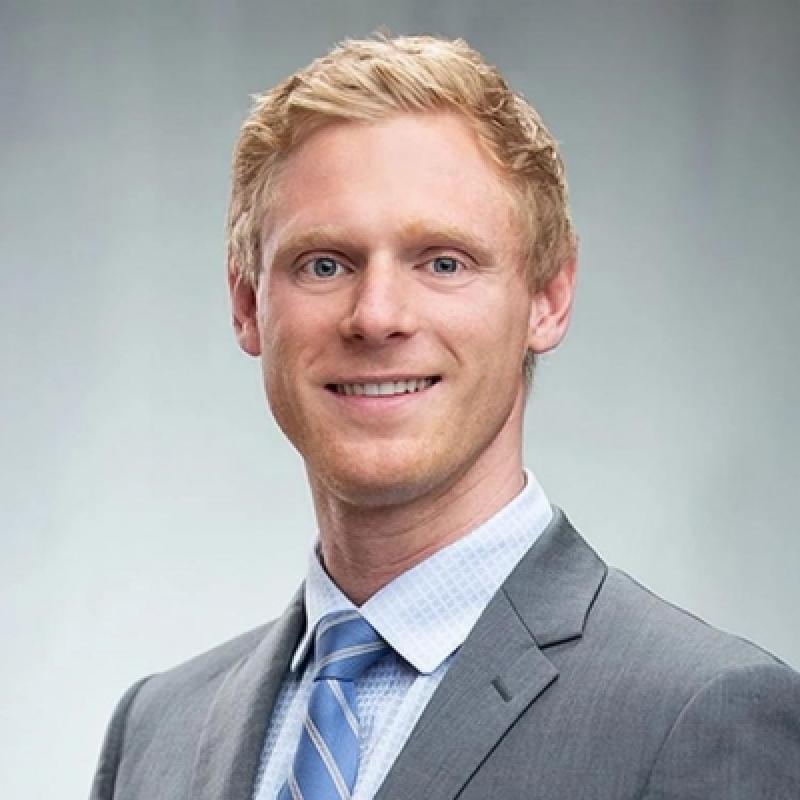
Burnaby, B.C.-based Vitacore Industries is launching Planet Impact, an ambitious Canada-wide recycling program targeting plastics and other materials that typically wind up in landfills.
This marks a significant strategic initiative on the part of Vitacore, which was launched in 2020 with the original mission to manufacture personal protective equipment (PPE) as a response to the onset of the pandemic.
Once the company saw the overwhelming proportion of masks and related materials was winding up in landfills, Vitacore decided to establish Canada's first-ever PPE recycling program in February 2021.
Now Vitacore is broadening the scope of its mission by embarking on its Planet Impact recycling campaign seeking to reduce the negative environmental impact of single-use PPE as well as other typically non-recyclable products.
The company will also be proceeding with plans to develop new technologies to recycle an ever wider variety of materials.
Extending Vitacore's recycling initiative
Via Planet Impact, an expanded number of hard-to-recycle products will be collected, broken down into their component polymer states and repurposed as pellets and other products.
"The vision of Planet Impact is to bring people and businesses together to create a sustainable future and eliminate waste." Mikhail Moore, president of Vitacore, said in a statement that accompanied the official Oct. 10 announcement of the new program.
"Our research and development of new recycling technology represents a massive step toward a truly circular plastics economy."
The launch of Planet Impact comes in the wake of a major expansion in the processing capacity of Vitacore's new plastic recycling plant in Port Coquitlam, B.C.
This is where masks and related PPE are disinfected, sorted, shredded, melted down and transformed into polypropylene pellets which are then repurposed into construction materials – such as concrete reinforcement – and textiles.
In April, Vitacore was awarded a grant of $900,000 from the provincial government's CleanBC Plastics Action Fund which enabled the company to upgrade its plant and equipment. It can now transform up to 12.5 million masks and respirators per month into reusable materials.
Vitacore's role as environmental steward
Vitacore was launched as a committed response to the onset of the pandemic. Led by Moore, a Canadian entrepreneur who previously headed up several engineering firms, it soon became the first Canadian N95 mask manufacturer authorized by Health Canada.
It did not take long before Vitacore discovered Canadian recycling facilities were refusing to accept used medical PPE – including its own masks – due to concerns over contamination. This gave Moore, who prides himself on "solving engineering problems and creating solutions that don't currently exist on the market," the idea to establish its Canadian PPE recycling program barely a year later.
In an interview with Sustainable Biz Canada, Moore explained the sequence of events that saw him help found Vitacore out of a concern for frontline workers and how Planet Impact enabled his company to pivot toward recycling.
"At the beginning of the pandemic we saw a need to support our front-line workers. That was what led us to assemble the amazing team that we have at our engineering firm and apply ourselves to the task of solving the problems faced by our front-line workers," Moore said.
"We identified the N95 respirator (as) the first problem we wanted to solve. And this led us to becoming the first Canadian company to be certified to manufacture N95s on home soil.
"But we were also aware that we were producing a single-use plastic product at a time when there is an ongoing effort to eliminate single-use plastic products. We recognized that this was a problem within the plastics industry and specifically within healthcare and PPE. We then set about addressing this matter."
Burnaby will be home to Vitacore's material science and biotech lab
Vitacore recently relocated its operations into a new 60,000-square-foot facility in Port Coquitlam, B.C., which is now home to the company's approximately 100 employees and serves as a combined manufacturing and recycling plant with growing emphasis on the latter.
"Right now the revenue is close to 50-50. If you would have asked us a year ago, it was 95 per cent manufacturing and only five per cent recycling," Moore said. "Now, recycling has taken off in a good way and we're starting to see lots of adoption of the programs that we've launched so far. We expect recycling to overtake our respirator manufacturing and PPE manufacturing over the next year."
Vitacore's new joint-purpose Port Coquitlam plant is merely the first stage in what Moore described as an "aggressive expansion plan". It will gradually branch out "into a few provinces" as part of an evolving process whereby it will establish new distribution centres and manufacturing facilities.
"We also have quite a few different partners across Canada, including institutional and research partners. McMaster University and the University of British Columbia have been two of our primary partnerships that started several years ago and are ongoing today," Moore said.
In the meantime, Vitacore is completing work on a parallel R&D facility in Burnaby that will include an advanced material science and biotechnology lab.
"We have a number of exciting updates that are going to be coming out over the next six months. These are all centred around innovation that we've created . . . within recycling that are intended to have as big of an impact as possible.
"That's really our goal moving forward – identifying key segments that are going to have a large impact and tackling problems big enough for us to want to pursue and dive into."
Vitacore aims to be at forefront of Canada's sustainable landscape
"Sustainability poses a large number of technical challenges and details that our team loves to dive into," Moore said. "Our passion about recycling is the same passion that drives us in other sectors, as well as solving problems that Canadians are encountering every day and which exist around the world."
"Right now the political landscape for recycling and sustainability as a whole is really changing . . . We have to make a very real and sustained difference in the way we operate our economies and in the way that we deal with input products.
"Recycling is a very important part of this process," Moore added. "We're starting to see . . . developments along those line across the provinces and at every level of government where more attention is being paid towards recycling and what really happens with our waste."
Moore believes this increasing level of government awareness and concern will lead to significant environmental progress and generate additional demand for circular economy products.
"There also needs to be pressure placed on manufacturers to start thinking about the full life cycle of a product and how we create that circular economy from start to finish," Moore said.
"Recyclers and waste disposal companies also need to be very serious about what they're saying that they're they're doing with products, and make sure that they are always thinking about the endpoint of products."