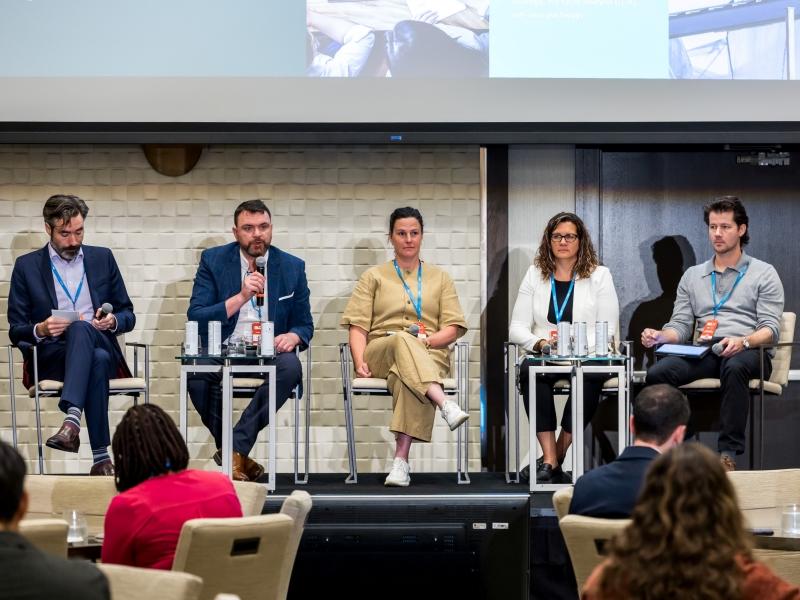
Developers and builders are paying more attention now than ever to the role embodied carbon plays in the pursuit of low-carbon or zero-carbon buildings.
Tackling the issue of embodied carbon was one of the main priorities at the recent Building Lasting Change Conference held by the Canada Green Building Council in Vancouver in June.
“Embodied carbon is playing a bigger role in our total carbon picture,” Iain MacFadyen, principal and owner with RGS Consultants, said during a panel at the three-day conference. (Embodied carbon in a construction project is the total greenhouse gas emissions linked to the building materials throughout the life of the building.)
“The thing to kind of understand when we're navigating through the embodied carbon picture is that there's multiple different components that build that up,” MacFadyen said.
To achieve net-zero carbon in a building, the materials that go into it must be considered. So too, must the waste that emerges either during renovation projects or eventual demolition, according to MacFadyen and others.
Concrete, steel, glass and insulation are among the building materials that require the most carbon input to source, produce and ship to construction sites.
“There's a balance that we need to strike when we're looking at embodied carbon versus operational carbon,” MacFadyen said. “We have to avoid carbon tunnel vision.”
Concrete courtyard planters a good example
Heather Reid, impact initiatives lead, sustainability with PCI Developments, provided an example around anticipating embodied carbon load.
While reviewing the courtyard design for a new condo building, she noticed it included concrete planter walls to provide separation between the courtyard and the residential patios. The planters were set on top of the roofing membrane, which meant that when the membrane needs to be replaced in 20 to 30 years, all the concrete planters would have to be torn up and then re-poured, adding to the overall carbon load of the building, Reid explained.
“My question is: is this captured in embodied carbon in our analysis (and) how much are we thinking about the renewal and maintenance over the service life available?”
Fellow panelist Jolene McLaughlin, vice-president of climate and sustainability at EllisDon, said concrete is a key issue to tackle. It provides opportunities to reduce embodied carbon through adjusting or reducing mixing formulas, setting times and total amount of concrete used in construction.
“We can extend the (concrete) cure time as long as it's not going to affect the schedule,” McLaughlin said. “That's going to have a huge carbon reduction. We can get the engineers to reuse supplementary, cementitious materials that decrease the carbon.”
Limberlost Place showcases mass timber solution
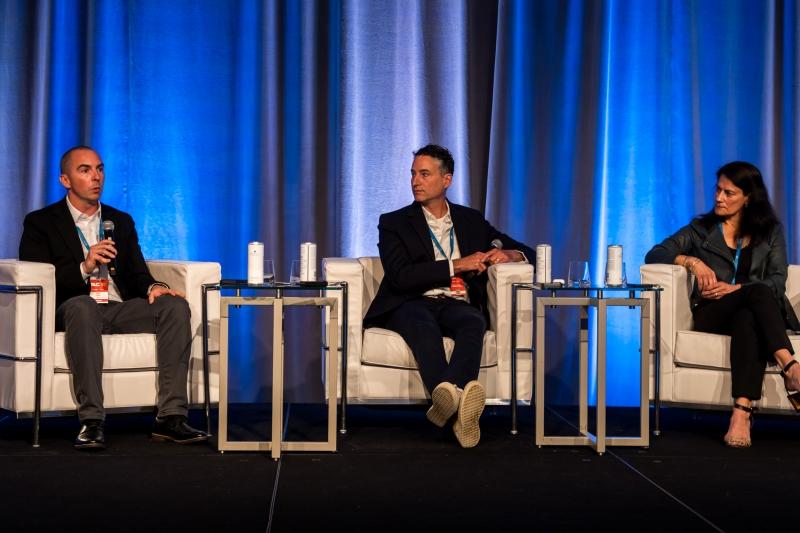
Mass timber, or cross laminated timber (CLT), is an increasingly successful option for large-scale residential or commercial construction that reduces the carbon load of a building by sequestering carbon within the wood.
Limberlost Place is a recently completed 10-storey mass timber academic building at George Brown College on Toronto’s waterfront.
A university might be the best place to showcase CLT because, by its nature, a school is a place of experimentation, learning and sharing, Nerys Rau, director of design and construction for Limberlost Place at George Brown College, said during a separate panel at the conference focusing on Limberlost as a case study.
"George Brown really wanted to be an example of what was possible,” she said, adding that the building is like having a living lab for students, faculty and visitors.
Designed by Toronto-based Moriyama Teshima Architects and built by PCL Construction, Limberlost Place was assembled with prefabricated CLT mass timber panels and prefabricated envelope panels, with a metal roof and steel lateral system. It's heated and cooled by the Lake Ontario Deep Lake Water Cooling System and uses natural ventilation designs and daylight harvesting with solar panels on the sloped roof.
Designer Philip Silverstein said the building operates nearly at Passive House energy standards. "There is a lot of wood in this building," Silverstein said. "I think a little over 4,000 cubic metres of timber. That's about three Olympic-sized swimming pools of timber fibre.”
He said U.S. and Canadian forests grow that much wood in about 12 minutes. The amount of carbon stored in the wood is equivalent to taking 1,100 cars off the road for one year, or the energy it takes to operate 550 homes for a year, Silverstein said. “That's a lot of carbon stored in that wood."
The building site, thanks to the pre-fabricated CLT panel system, required fewer workers, less clutter and much less waste, Mike Love, senior superintendent with PCL Construction, said. The CLT panel sections were lowered into place and connected without cutting on site.
The structure was out together during the winter of 2022 and 2023, which meant the wood would often get wet. That's not a big deal, Love said. "The wood is allowed to get wet. It's not going to melt."
He said they developed strategies to ensure the wood dried out as needed without hindering their process. “It was important to let the wood breathe.”
Limberlost, at 10 storeys, will likely motivate other municipalities around the country to permit for taller, larger timber structures, the design team said, noting that more than 400 local, national and international groups have toured the space, including during the construction process.