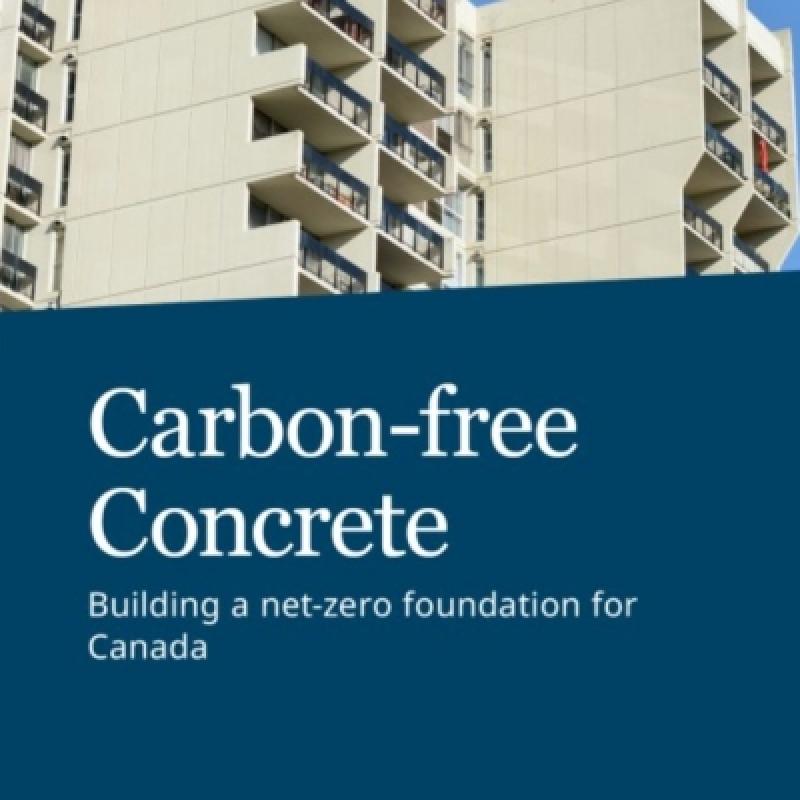
A new study by the Pembina Institute calls on federal and provincial governments to ramp up procurement policies to stimulate production of low-carbon concrete in Canada.
Entitled Carbon-free Concrete: Building a net-zero foundation for Canada, the report hopes to raise awareness about the ways and means to decarbonize a concrete industry that is responsible for eight per cent of global carbon emissions.
Pembina, a national non-partisan energy think tank dedicated to advancing climate solutions in Canada, has long been an advocate for policies promoting the transition to clean energy.
Focusing on the hard-to-abate concrete sector, the report underscores how the industry has been slow or otherwise reluctant to innovate, and the need for governments to incentivize concrete producers to invest in technological changes to lower their carbon footprint.
"We have seen on the federal level that a roadmap has been issued to help the concrete industry get to net-zero by 2050, so there's great ambition and a plan to take us there, but we don't have a sense of how these milestones will be met and how we will reach these targets," Rachel Sutton, co-author of the report, said in an interview with Sustainable Biz Canada.
"We wanted our report to serve as a call to action for governments to (pursue) 'buy clean' policies, establish an embodied carbon standard, and support that standard so that when these products become available, there will be a minimum level of demand for low-carbon concrete that will incentivize the industry to decarbonize."
Three key measures to reduce carbon intensity of concrete
The report focuses on three jurisdictions - British Columbia, Ontario, and the Government of Canada - "where cement production has a significant economic impact and budget implications, and existing policies already encourage industry investment in zero-emission alternatives."
The report identified several main avenues as having the potential to spur meaningful carbon reductions within the industry, including the need for "design optimization" by updating building codes calling for lower embodied carbon; upgrading of production facilities and equipment to accommodate lower-carbon fuel sources; and using carbon capture and storage.
"CCUS (carbon capture, utilization and storage) is currently the only option for eliminating process emissions and has the potential to capture more than 90 per cent of the greenhouse gases emitted from cement kilns," according to the report.
Substituting fly ash and slag for clinker
One of the most direct methods of lowering emissions in the concrete sector involves reducing the amount of "clinker," the primary, energy-intensive ingredient in cement which typically comprises 10 to 15 per cent of concrete by volume.
Although clinker serves as the essential strength-contributing ingredient of concrete, it also accounts for 90 per cent of total carbon emissions generated by concrete production.
This is due to the highly polluting "sintering" process whereby limestone and aluminosilicate materials such as clay are heated at temperatures of 1,400 C to 1,500 C in a rotary kiln and fused to the point of liquefaction to produce clinker. The clinker is then finely ground and mixed with gypsum (ensuring compressive strength) to produce cement.
According to the report, increasing the proportion of fly ash and slag relative to clinker in cement would result in meaningful reductions in the carbon footprint of a cement production process mired in centuries-old, carbon-emitting production methods.
"Clinker is the main binding agent that goes into cement and the production of clinker is highly carbon-intensive because of the combustion process it undergoes. Reducing clinker and changing the cement mix are the keys to lowering those emissions," Sutton said.
Procurement policies and performance standards
The study also concludes that federal and provincial governments need to embrace procurement strategies that prioritize low-carbon concrete by committing to purchase a minimum amount of new concrete products coming onto the market. This would create a stable market and incentivize the industry to invest in new decarbonization technologies.
"What we have found is that the major reason the industry is (not switching to clinker alternatives) is that there's simply no demand for this new product," Sutton explained.
"This is why we need government procurement strategies and 'buy clean' policies to send a signal to the industry that there's someone actually asking for this product to be brought onto the market.
"The industry has shown that these product options are available but, like in any industry, unless they have actual buyers looking to purchase this variation, there's little incentive to start investing in new production methods."
Instead of prescriptive regulations, the report also suggests the industry would be better served by performance-based standards allowing producers to find their own pathways to low-carbon concrete production.
"It's going to take a culture change (to decarbonize the industry). We have been producing concrete the same way for over 200 years and change has been slow. Builders and architects are accustomed to designing buildings with one kind of concrete product their entire career," Sutton said.
She is hopeful the report will play a significant role in helping educate and build awareness among all stakeholders that these new lower-carbon products exist and are both reliable and viable.