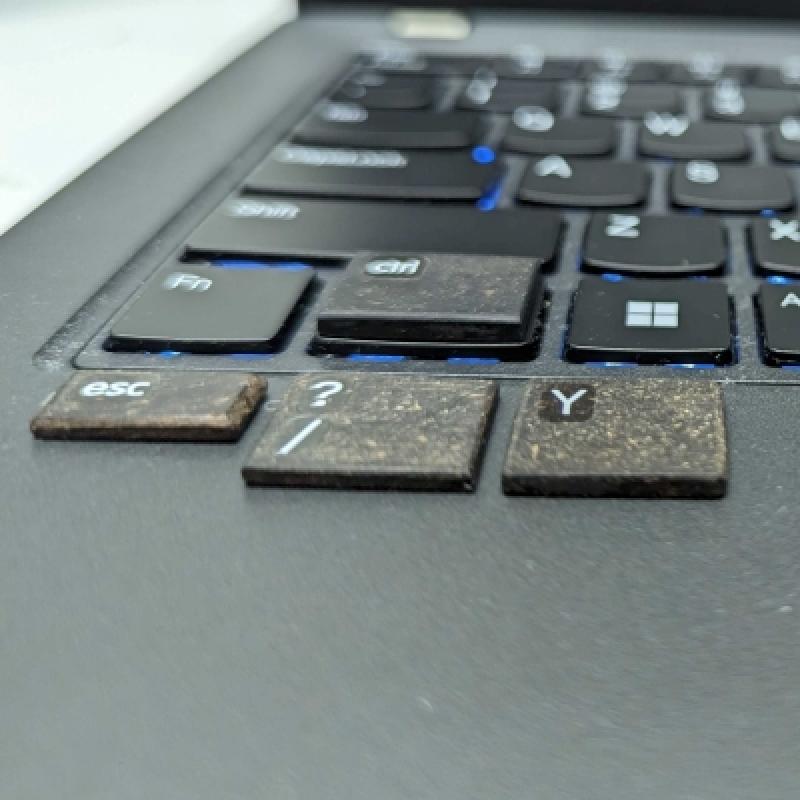
Montreal-based tech start-up Agapyo is entering a new phase in the development of its "jam" product, a mouldable and biodegradable alternative to conventional petroleum-based ABS (acrylonitrile butadiene styrene) plastic.
The novel and patented chemical process involved in the manufacture of jam was initially developed at a Canadian university, after which Agapyo acquired an exclusive license to develop and market the technology.
Jam is a 100 per cent plant-based sustainable thermoplastic resin which has the potential of serving as a natural replacement for petroleum-based ABS plastic in the manufacture of thousands of consumer products. Up until now, there have been no viable green alternatives.
Agapyo has begun outsourcing the sampling and testing of jam to Toll manufacturers following the award of $300,000 in grants by the Quebec Climate Solutions Festival to Dr. Monika Rak, Agapyo co-founder and technical lead, in recognition of her scientific work.
By relying on Toll manufacturers to produce samples for research and pilot testing, Agapyo will be able to further refine its bioplastic jam without the need for large-scale capex. It will also ensure the product meets the specifications required by target industries involved in the manufacture of consumer electronics, automotive parts and home appliances.
First launched in 2022, the company expects to set up its own pilot production line within the next two to three years with an annual capacity of about 200 tonnes. Agapyo will then be in a position to begin supplying the multi-use, rigid plastics market at scale and harness the potential for the greening of a notoriously hard-to-abate industrial sector.
Making inroads into the rigid petro plastic market
"We want jam to be a product that leads the way in the field of sustainable, rigid plastic alternatives. Right now, bioplastics is a market that is growing and gaining a lot of traction as well as awareness," Alina Grenier-Arellano, Agapyo co-founder and product lead, said in an interview with Sustainable Biz Canada.
"Jam is a rigid petro plastic replacement and today there are very few options available for companies which may be in the process of choosing alternative green materials for product housings and electronic housings such as those found in your car, your monitor, your webcam, your computer peripherals and your speaker system.
"These are areas we foresee our product as becoming a viable, scalable and cost-effective sustainable alternative to some of the rigid plastic products that we have become completely used to."
Altering the chemical structure of wood polymer
Agapyo's standalone jam product differs from other bioplastics primarily due to its scalability and unique chemical structure. Unlike many bioplastics that are not scalable, jam is designed to be manufactured at volume, making it viable for industrial applications.
The critical innovation ushered in by Rak involves a new method of altering the chemical structure of lignocellulose, a polymer found in wood, so that it melts rather than burns when heated.
"Instead of having a material or a molecule that burns very fast because there's a zipper effect, we've created a little bit of space within the lignocellulose structure to allow for moulding to take place.
"We are able to (apply our technology) in a way that is replicable and scalable, so we can manufacture jam at volume," thereby overcoming the kinds of inherent limitations found in "most bioplastics," according to Grenier-Arellano.
Although the manufacturing technology developed by Agapyo could well have applications to other plastic products beyond the replacement of rigid ABS plastics, the company wants to maintain a narrow strategic focus for the foreseeable future.
"As a startup, it's so important to stay focused on where you're going. However, we have seen some results that have enhanced our flexibility . . . For example, would we want to target plastic bags? No. But maybe we would want to look at developing alternatives to running shoe plastic or textile plastic in the future.
"Right now, there's a need in the rigid petro plastic market, and there are no (alternative sustainable) solutions right now for rigid petro plastics - so that is where we want to live," Grenier-Arellano said.
Agapyo team driven by shared passion for sustainability
Agapyo came into being through the venture studio model run by Tandem Launch, a unique startup foundry and seed fund also based in Montreal, which specializes in tech transfer of novel, patentable technologies from Canadian universities to the market.
In addition to Grenier-Arellano, who oversees the manufacturing of jam, Agapyo is also led by Rak, noted for her previous work with carboxylated nanocrystals and her passion for environmental sustainability, and Jeff Costas, the company CEO, who previously had extensive experience in manufacturing large lithium batteries for ships in the U.S.
"Monica (Rak) very much loves to call herself a tree hugger and everyone on the team has, in fact, been an impact entrepreneur before - Jeff in lithium batteries, Monica in carboxylated nanocrystals - while I worked in a social impact family business beforehand where we sold games to social and mental health centres across Canada," Grenier-Arellano explained.
"So I had that manufacturing experience and that's why I was so inspired when I found this opportunity to join the team. I wanted to help develop jam as a solution for a world that sees us living among plastic every day, all the time . . . We want to be part of the process where future generations will not be living with microplastics."